Attendance
- Fletcher
- Hunter
- Evan
Journal
Tasks
- Get the IR autonomous finished
- Driver Practice
- Prepare the field for pack up
Reflections
We started the day by working on the IR autonomous. Fletcher had already done some work on it, though the surface he had done the testing was quiet slippery and all the work he had done had to be redone. The calibration was done in a system of checking and adjusting where Fletcher would run the autonomous and Evan or Hunter would tell him how off of the target it was. Fletcher would then change the code based on their observations. One challenged we faced in this is robot placement. Some inaccuracies in robot placement, which was 21″ from the left wall [depicted] could cause the autonomous to fail. To lessen this problem, we made a stick that is 21″ in length.
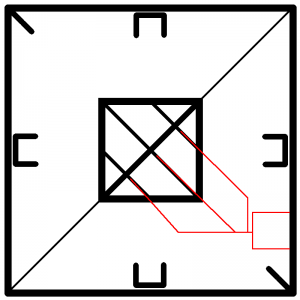
We applied our check and adjust system to each of the three paths that could be taken. The rightmost path was particularly difficult because unlike the other two cases, it had three stages rather than two. The other two went forward for a little bit, turned and went forward again and put the ring on. The dextral path went forward a small amount, turned 90 degrees, went forward an amount, turned, went forward again, and put the ring on. While working on the right path, we were encountering problems with the robot being slow, which degraded the ability of our autonomouses, so we changed the batteries and fixed this problem. This all took from about 11:00 to 4:00 with lunch (where the pizza man drew a robot for us on the box!).
Once we finished the autonomous, we moved on to driver practice. In it, we found that the ideal place for the robot to rotate to put itself in the ideal place to get the ring is between the mechanism for moving the hand left and right and the tube that holds the hand on. We also found that if when removing a ring from a dispenser or when putting a ring on a peg we use the device to move the hand vertically to grab the ring or to let go of the ring (this is as apposed to doing this with the scissor lift).
Once driver practice was done, we started playing with the fork lift. We lowered the fork and put a skateboard, a spool of wire, a drill, and a bottle of Pepsi on it and lifted it, first with the peg assist, then after we got too high for the peg assist, just with the scissor. Sadly, this put too much strain on the scissor lift and bent several of the pieces on the lower portion and bent one in particular quiet badly in three place. Luckily, Evan was able too take the robot hame after this and replace the sections of the scissor lift with steel.
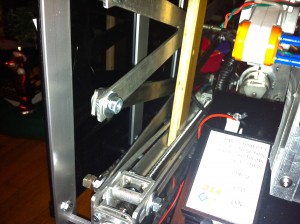